In the age of digitalization, terms such as additive manufacturing (AM) or 3D printing have also arrived in the world of technical ceramics. We at Steka have been dealing with this topic for about 10 years and even though these processes are far from being as established as, for example, 3D printing of plastics or metals, we already assume that certain additive shaping processes in the field of technical ceramics will experience a breakthrough by 2025.
We would like to present the most important processes from our point of view here and highlight the main differences as well as advantages and disadvantages for future products of our customers.
We would like to take a closer look at the following processes:
• LDM Liquid Deposition Modeling
• Binder Jetting
• LCM Lithography based Ceramic Manufacturing
LDM (Liquid Deposition Modeling)
a. Shaping process:
Ceramic raw material is moistened and pre-compacted e.g. via extruders. This mass is then applied to a plate using a printer e.g. of the Italian manufacturer WASP so the part is built up layer by layer.
b. Preparation for sintering:
The finished component is dried very carefully and can be processed very well in the so-called green state.
c. Sinter firing
The firing process at the appropriate temperature for the material in question has no other special features and results in the actual ceramic component.
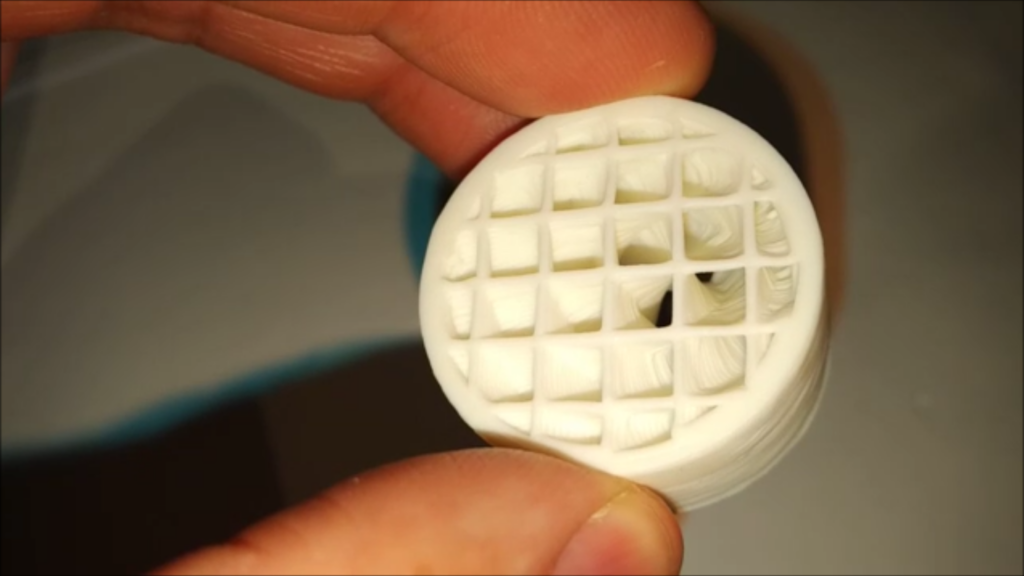
This process is by far the most favorable manufacturing process in the field of additive manufacturing. Common ceramics are clay, earthenware and porcelain, also aluminumoxide and zirconium oxide are already being processed in the field of technical ceramics. The structures are relatively coarse and are particularly suitable for architecture (facade elements) or art. In the field of technical ceramics, there are fewer applications for such components.
Binder Jetting
a. Forming process:
This relatively old printing process involves the layer-by-layer bonding of powdered ceramic raw material to form a component. Similar to an inkjet printer, a printer head is passed over a powder bed.
b. Preparation for sintering:
The finished component must be cleaned and, depending on the type of adhesive, the binder must be removed by various methods. This is done, for example, with a debinding oven.
c. Sinter firing:
Depending on the size and shape of the component, special kiln furniture and supports may be required; otherwise, ordinary firing takes place at the temperature suitable for the material in question.
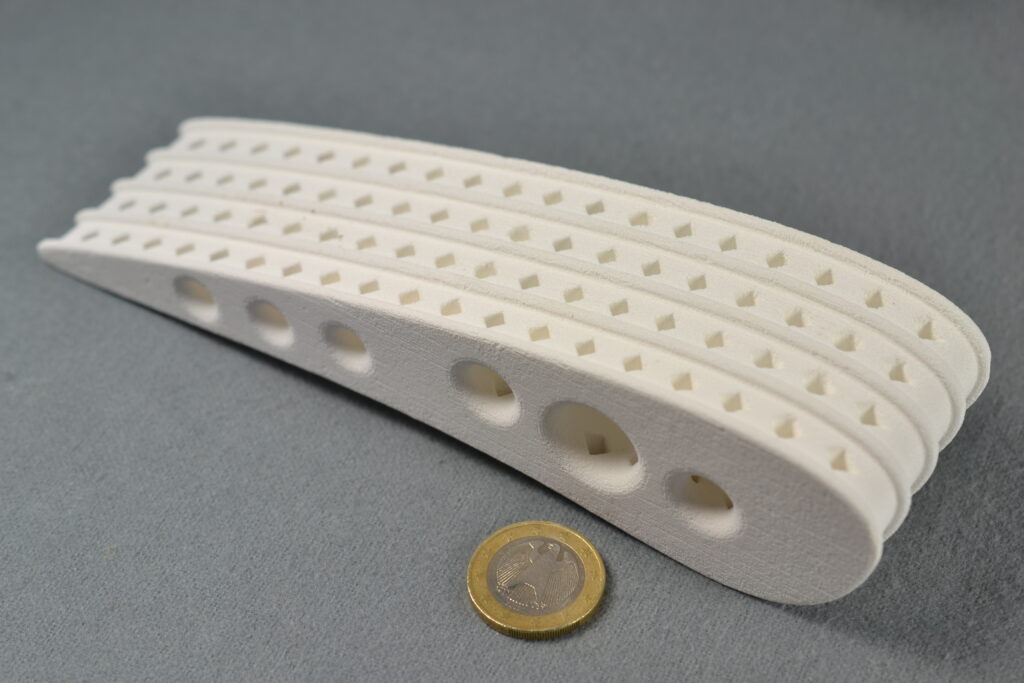
This process, like the LDM process, has visible layers and is therefore rather porous. However, very complex and large-scale structures can be produced, but these are less in demand in the field of technical ceramics.
LCM (Lithography based Ceramic Manufacturing)
a. Shaping process:
A component is built up layer by layer from a suspension applied to a translucent plate in which the component is immersed. Depending on the hardware manufacturer, each individual layer is hardened with a directed laser or optically directed light spots.
b. Preparation for sintering:
The UV sensitive parts must only be processed and manipulated in a UV free environment prior to firing, this is usually made possible with yellow light. Cleaning of the parts with different methods can be done manually or in an automated process, depending on the requirements. Subsequently, debinding takes place, e.g. in a dedicated debinding oven. The filigree structure is now placed on kiln furniture in the sintering furnace.
c. Sinter firing:
Depending on the shape of the component, suitable sintering aids and appropriate positioning of the parts in the furnace are decisive factors. The firing curve and temperature depend on the requirements of the ceramic material.
This process can confidently be described as the most expensive. In addition to the elaborate hardware, the costs for the respective suspension, which are specially produced for the respective ceramic materials, should not be underestimated. For particularly small parts in the field of technical ceramics, this process seems most likely to gain in importance for our customers. The advantages for our customers lie in the almost limitless design process. Undercuts and cavities give new freedom to the designer.
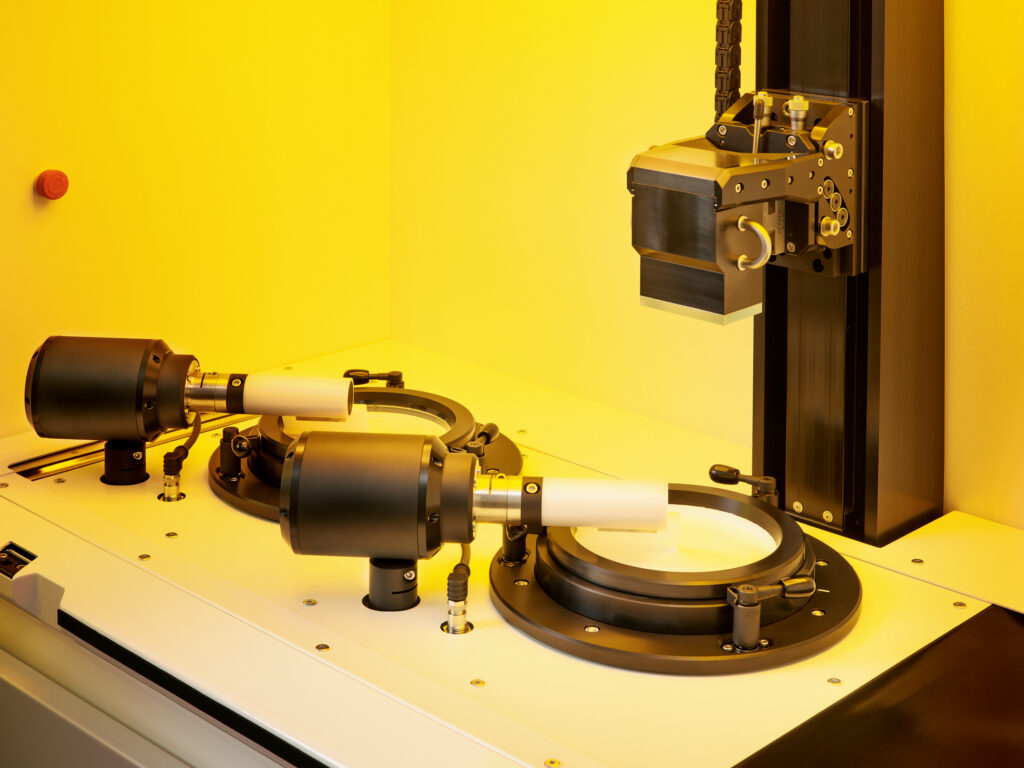

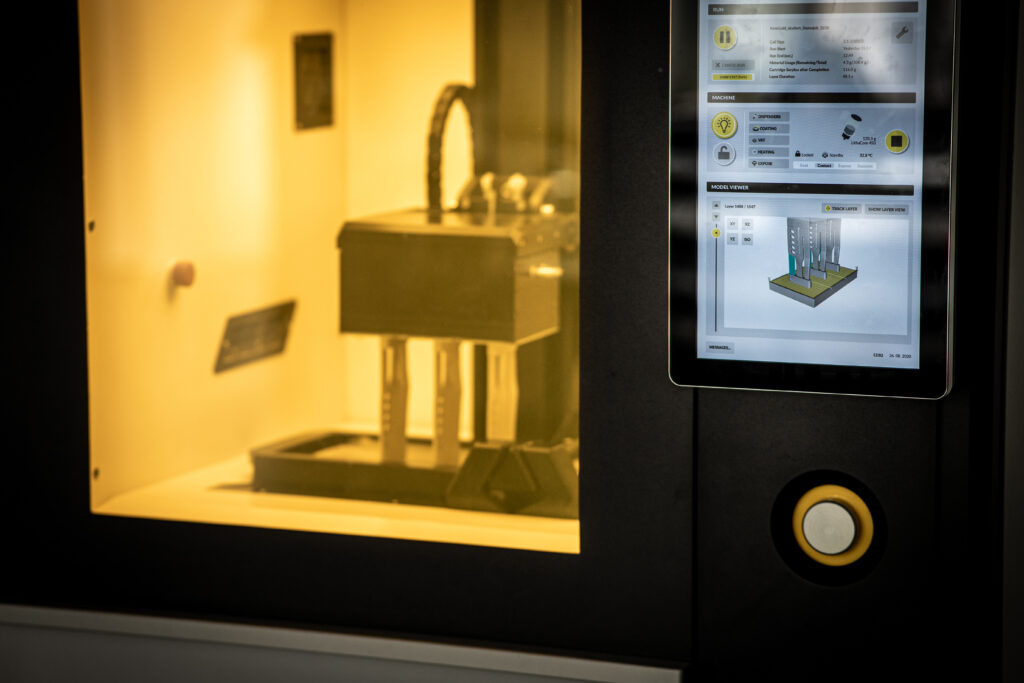
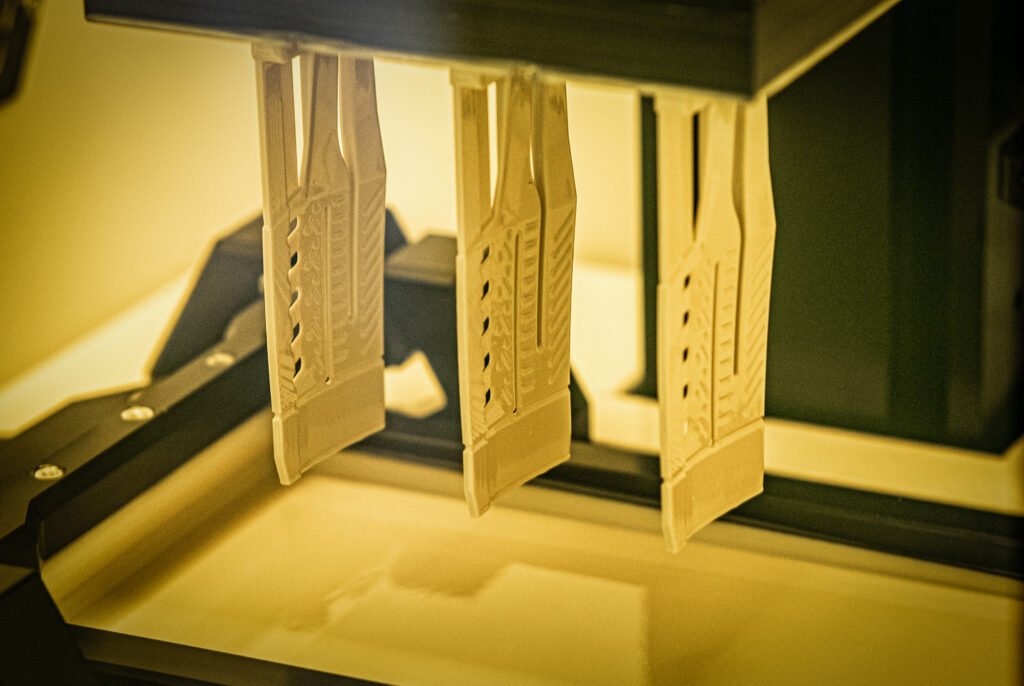
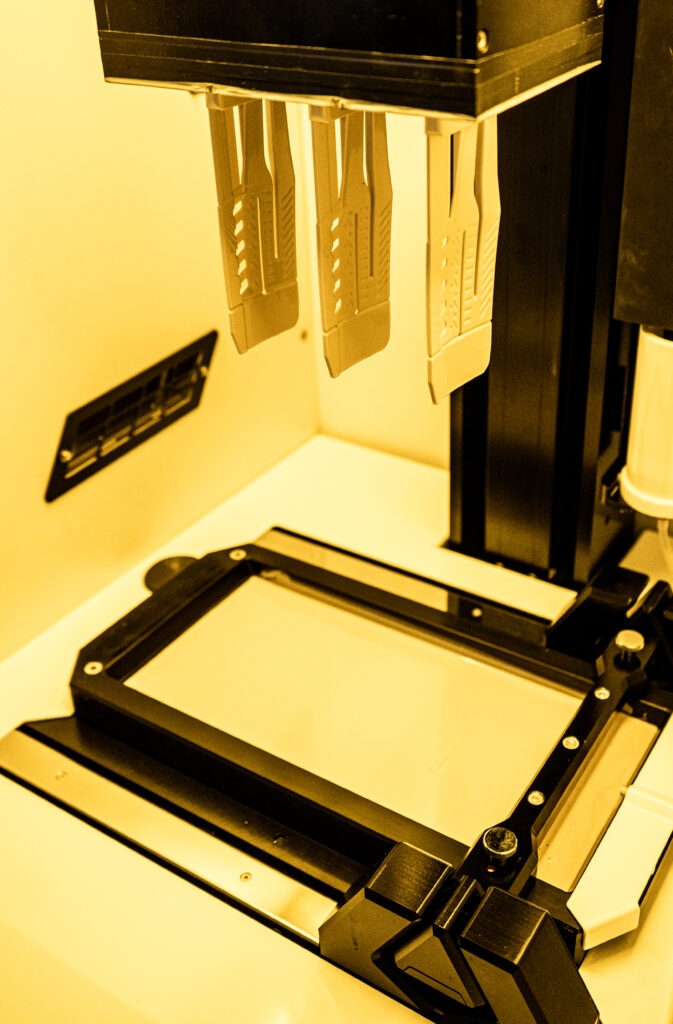
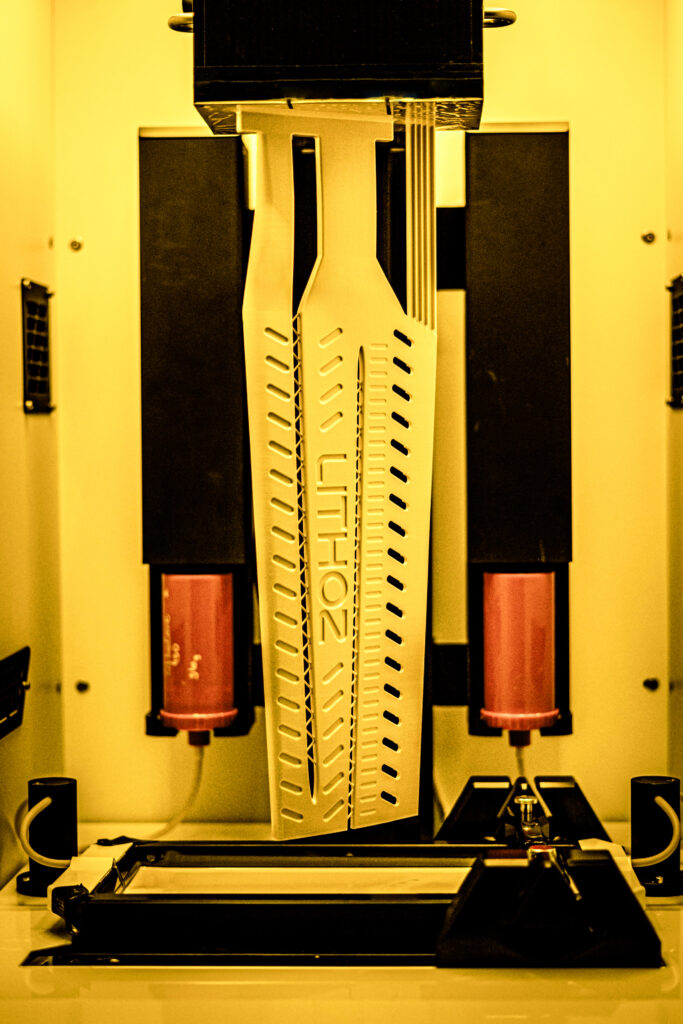
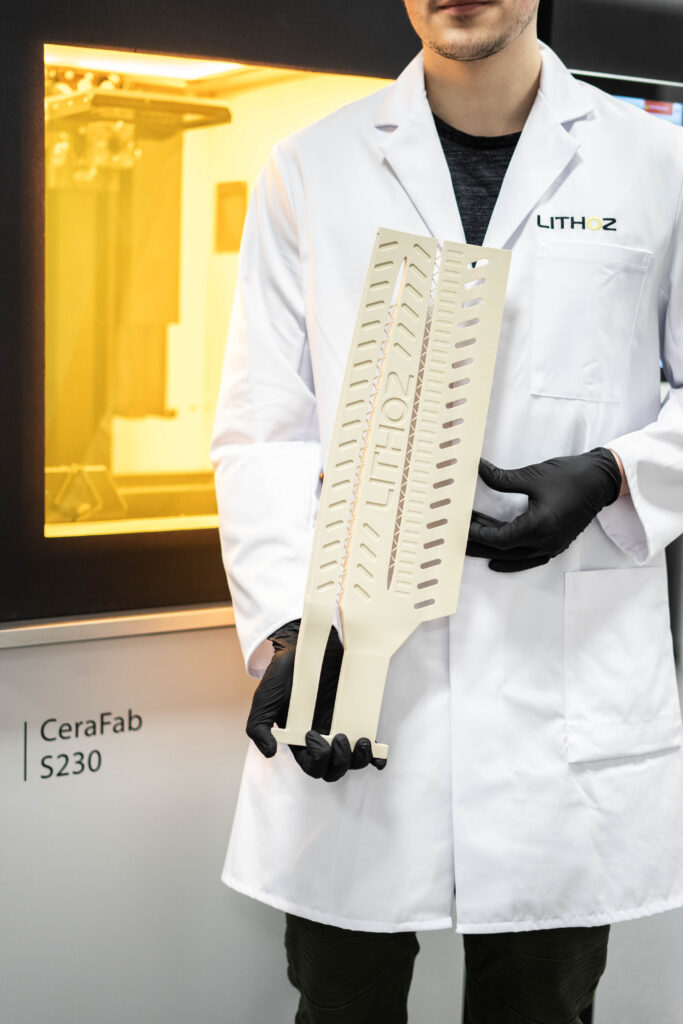
The advantages
For our customers, however, the most important advantages are those that only become apparent in the course of product development, namely when several partly different components can suddenly be combined into a single part, thus simplifying the procurement of different materials and components as well as the assembly processes quite considerably. For example, a component can contain an insulator, a heat sink, a mounting bracket, threaded holes, a strain relief and much more. The imagination in the design development process is thus given much more freedom. Finally, if something changes later in the design, only the 3D CAD file in STL format needs to be adjusted, there are no tooling costs.
We are looking forward to working with our customers and partners to explore the possibilities of these manufacturing processes, which are now already very advanced, and in the mid-term ready to be implemented at Steka for series production. In the meantime, we are working on our know-how in this area in our network of hardware manufacturers and research institutes as well as service providers for the production of prototypes and look forward to new challenges that are presented to us as experts in the production of technical ceramics.
The pictures were provided by WZR ceramic solutions GmbH (LDM & Binder Jetting) and Lithoz GmbH (LCM).