Begriffe wie Additives Fertigungsverfahren oder additive manufacturing (AM) beziehungsweise 3D-Druck sind im Zeitalter der Digitalisierung auch in der Welt der technischen Keramik angekommen. Wir bei Steka beschäftigen uns seit etwa 10 Jahren mit diesem Thema, und auch wenn diese Verfahren noch längst nicht so etabliert sind wie etwa 3D-Druck von Kunststoffen oder Metallen, gehen wir davon aus, dass bestimmte additive Formgebungsverfahren im Bereich technischer Keramik bis 2025 einen Durchbruch erleben werden.
Wir möchten hier die aus unserer Sicht wichtigsten Verfahren vorstellen und die wesentlichen Unterschiede sowie Vor- und Nachteile für künftige Produkte unserer KundInnen herausstreichen.
Auf folgende Verfahren gehen wir näher ein:
• LDM Liquid Deposition Modelling
• Binder Jetting
• LCM Lithography based Ceramic Manufacturing
LDM (Liquid Deposition Modelling)
a. Formgebungsprozess:
Keramisches Rohmaterial wird angefeuchtet und z.B. über Extruder vorverdichtet. Anschließend wird diese Masse mit Hilfe eines Druckers – etwa von dem italienischen Hersteller WASP – auf eine Platte aufgetragen und das Bauteil schichtweise nach oben aufgebaut.
b. Vorbereitung zum Sintern:
Das fertige Bauteil wird sehr behutsam getrocknet und kann im sogenannten Grünzustand sehr gut bearbeitet werden.
c. Sinterbrand:
Der Brennprozess in der für das jeweilige Material geeigneten Temperatur weist keine sonstigen Besonderheiten auf und ergibt das eigentliche Keramikbauteil.

Dieses Verfahren ist mit Abstand das günstigste Herstellungsverfahren im Bereich der additiven Fertigung. Übliche Keramiken sind Ton, Steingut und Porzellan, es werden aber im Bereich technischer Keramik durchaus schon Aluminiumoxid und Zirkonoxid verarbeitet. Die Strukturen sind relativ grob und eignen sich ganz besonders für die Architektur (Fassadenelemente) oder Kunst. Im Bereich der technischen Keramik finden sich eher weniger Einsatzgebiete für solche Bauteile.
Binder Jetting
a. Formgebungsprozess:
Bei diesem schon relativ alten Druckverfahren handelt es sich um ein schichtweises Verkleben von pulverförmiger keramischer Rohmasse zu einem Bauteil. Ähnlich wie bei einem Tintenstrahldrucker wird ein Druckerkopf über ein Pulverbett geführt.
b. Vorbereitung zum Sintern:
Das fertige Bauteil muss gereinigt und je nach Art des Klebers mit unterschiedlichen Verfahren vom Binder befreit werden. Dies erfolgt z.B. mit einem Entbinderungsofen.
c. Sinterbrand:
Je nach Größe und Form des Bauteils werden eventuell spezielle Brennhilfsmittel und Stützen benötigt, ansonsten findet ein gewöhnlicher Brand mit der für das jeweilige Material geeigneten Temperatur statt.
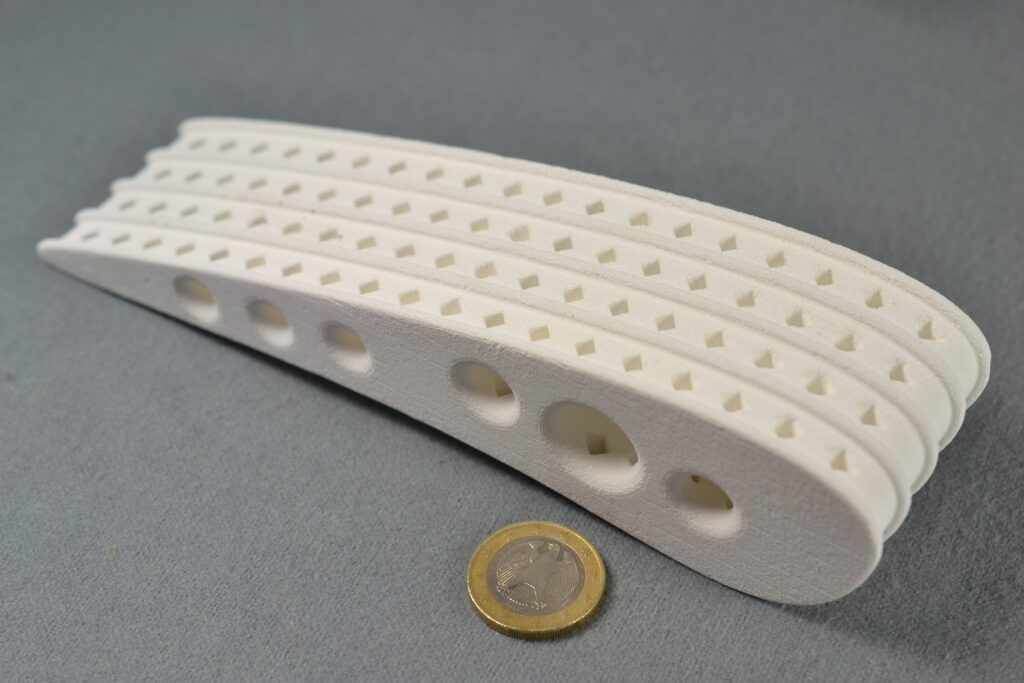
Diese Methode weist wie das LDM-Verfahren sichtbare Schichten auf und ist daher eher porös. Es können aber sehr komplexe und großräumige Strukturen hergestellt werden, die aber im Bereich technischer Keramik eher weniger gefragt sind.
LCM (Lithography based Ceramic Manufacturing)
a. Formgebungsprozess:
Hier erfolgt der schichtweise Aufbau eines Bauteils aus einer Suspension, die auf einer transluzenten Platte aufgetragen und in die das Bauteil eingetaucht wird. Je nach Hersteller wird jede einzelne Schicht mit einem gerichteten Laser oder optisch gerichteten Lichtpunkten erhärtet.
b. Vorbereitung zum Sintern:
Die UV-empfindlichen Teile dürfen vor dem Brand nur in einer UV-freien Umgebung bearbeitet und manipuliert werden, dies wird üblicherweise mit Gelblicht ermöglicht. Die Reinigung der Teile mit unterschiedlichen Methoden kann je nach Erfordernis manuell oder im automatisierten Prozess erfolgen. Anschließend erfolgt das Entbindern z.B. in einem eigenen Entbinderungsofen. Die filigrane Struktur wird jetzt auf Brennhilfsmitteln in den Sinterofen eingebracht.
c. Sinterbrand:
Je nach Form des Bauteils sind geeignete Sinterhilfen und die geeignete Positionierung der Teile im Ofen entscheidende Faktoren. Die Brennkurve und Temperatur richtet sich nach den Erfordernissen des keramischen Werkstoffs.
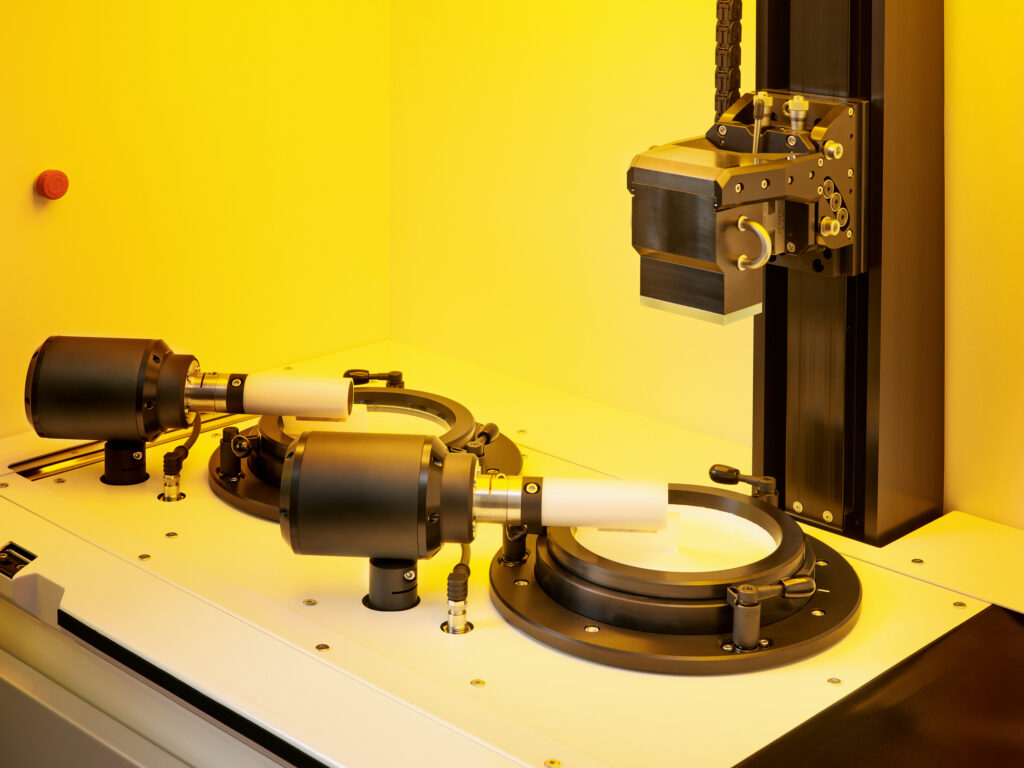
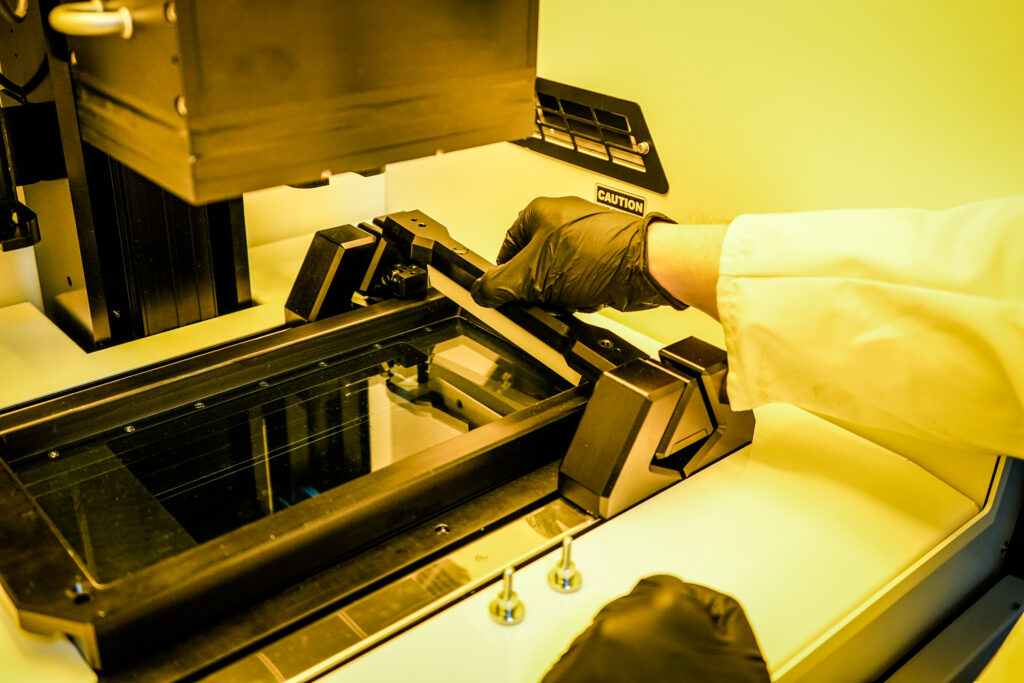
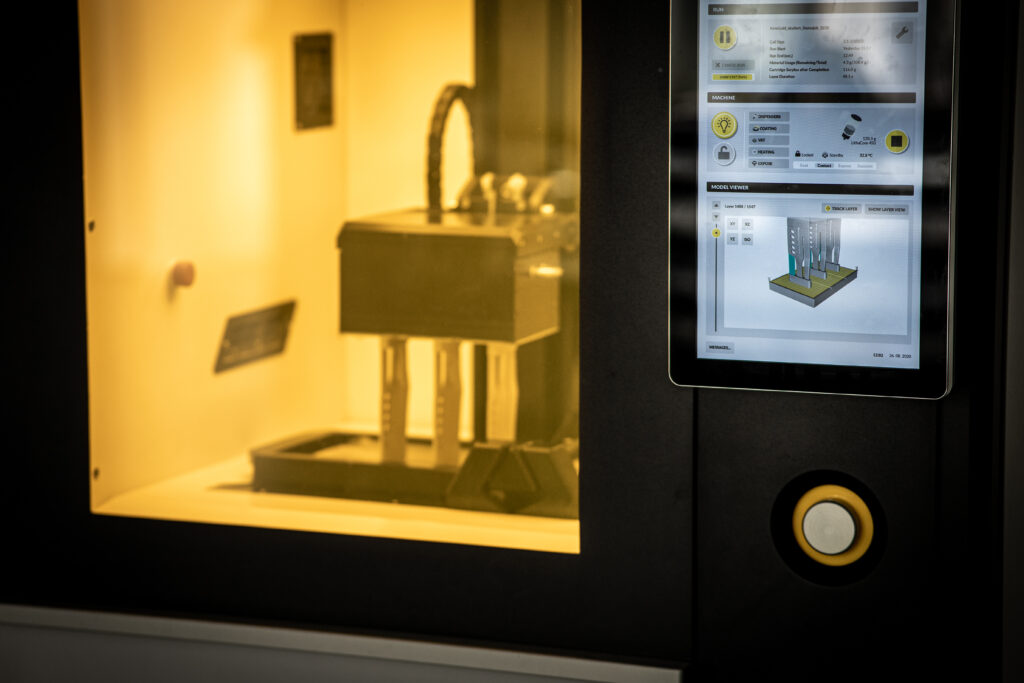
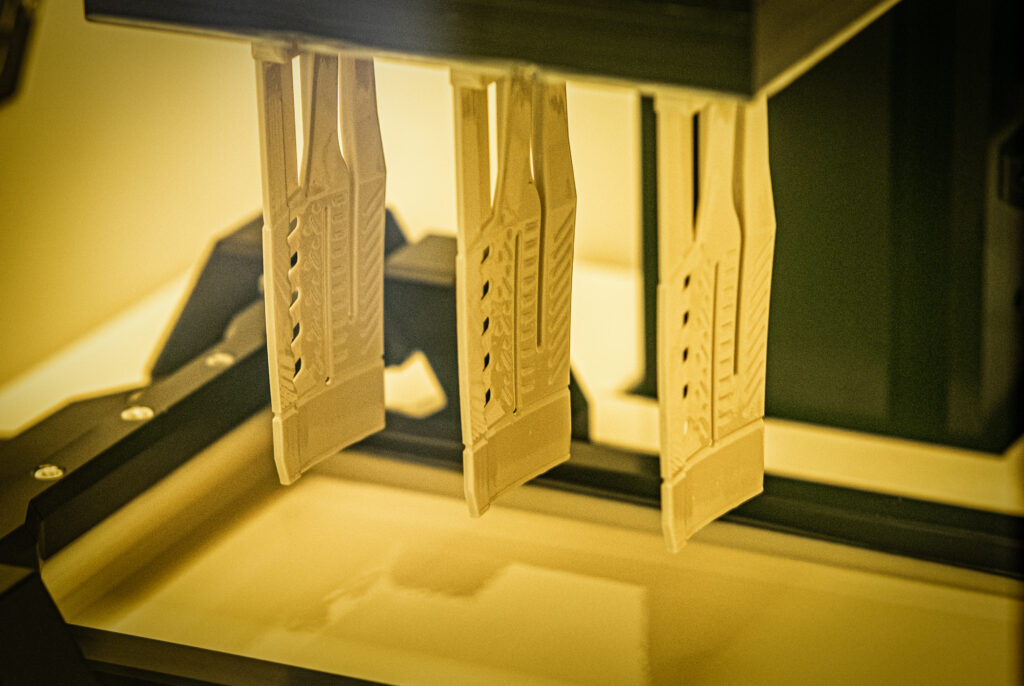
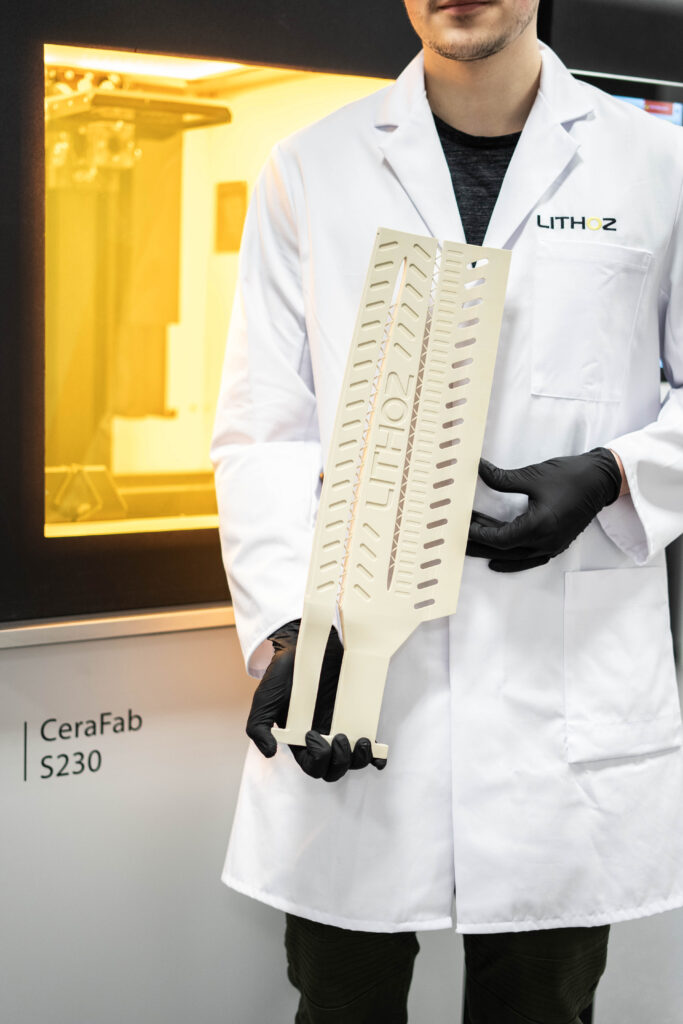
Dieses Verfahren kann getrost als teuerstes bezeichnet werden. Neben der aufwendigen Hardware sind die Kosten für die jeweilige Suspension, die eigens für die jeweiligen keramischen Werkstoffe hergestellt werden, nicht zu unterschätzen. Für besonders kleine Teile im Bereich technischer Keramik erscheint dieses Verfahren für unsere KundInnen am ehesten an Bedeutung zu gewinnen. Die Vorteile liegen im fast grenzenlosen Designprozess. Hinterschneidungen und Hohlräume geben der Konstruktion neue Freiheiten.
Die Vorteile
Ganz wesentlich sind aber für unsere KundInnen Vorteile, die sich erst im Zuge der Produktentwicklung zeigen, dann nämlich, wenn plötzlich mehrere teils verschiedene Bauteile zu einem einzigen Bauteil vereint werden können. Damit können die Beschaffung unterschiedlicher Materialien und Komponenten sowie die Montageprozesse ganz wesentlich vereinfacht werden. Ein Bauteil kann z.B. einen Isolator, einen Kühlkörper, eine Halterung, Gewindebohrungen, eine Zugentlastung und vieles mehr enthalten. Dem Designentwicklungsprozess stehen damit viel mehr Freiheiten zur Verfügung. Sollte sich schließlich später im Design etwas ändern, ist lediglich die 3D-CAD-Datei im STL-Format anzupassen, es entstehen keine Werkzeugkosten.
Wir freuen uns darauf, zusammen mit unseren KundInnen und PartnerInnen die Möglichkeiten dieser jetzt schon sehr weit fortgeschrittenen Fertigungsverfahren zu erforschen und sie mittelfristig auch bei Steka für eine Serienfertigung zu implementieren. In der Zwischenzeit arbeiten wir in unserem Netzwerk aus Hardwareherstellern und Forschungsinstituten sowie Dienstleistern für die Herstellung von Prototypen an unserem Know-how in diesem Gebiet und freuen uns auf neue Herausforderungen, die an uns als ExpertInnen für die Herstellung technischer Keramik herangetragen werden.
Das Bildmaterial wurde dankenswerterweise von WZR ceramic solutions GmbH (LDM & Binder Jetting) und Lithoz GmbH (LCM) zur Verfügung gestellt.