Silicate ceramics are with us in everyday life and are also frequently used in industry: in household appliance technology they are used to isolate electrical connections, thermoelements and thermostats. In energy supply, silicate ceramics are used in shunt reactors or low-voltage high-performance fuses. Porous silicate ceramics are used, among other things, in electric heating technology – for example in heating elements. The reasons for the popularity of the material are varied: silicate ceramics are very resistant, can withstand extreme temperatures as well as UV light and corrosion and can be exposed to high mechanical loads.
Oxide ceramics have similar positive character properties. In times of climate warming and the current energy crisis, it is worth comparing the two materials. How do silicate and oxide ceramics fare in terms of energy efficiency?
- The raw materials for the production of silicate ceramics, powders or granulates, are produced directly from natural, mineral raw materials, are recyclable and under certain circumstances even biocompatible. Oxide ceramics consist of synthetic materials, which are obtained, for example in the case of aluminum oxide, from bauxite in a complex chemical process and calcined in special kilns at around 1,000°C. In comparison to oxide ceramics, the production of ceramic masses for silicate ceramics requires far less energy and produces less CO2 emissions, as only energy is required for the production of the spray corn for evaporating the slurry.
- The sintering temperature of silicate ceramics is generally lower than that of oxide ceramics. This makes the production of silicate ceramics more energy efficient, as the sintering process – the conversion from mineral mixture to dense ceramic – starts at a temperature of around 900°C. The sintering process is completed with silicate ceramics upon reaching a temperature of around 1,300°C, and a certain holding time at this temperature. Oxide ceramics often require temperatures of 1,600 to 1,800°C. This inevitably leads to higher CO2 emissions.
- Another plus is that silicate ceramics generally have better heat storage capacity and low thermal conductivity, making them a good choice for heat exchangers and heat storage. Less heat loss means higher energy efficiency.
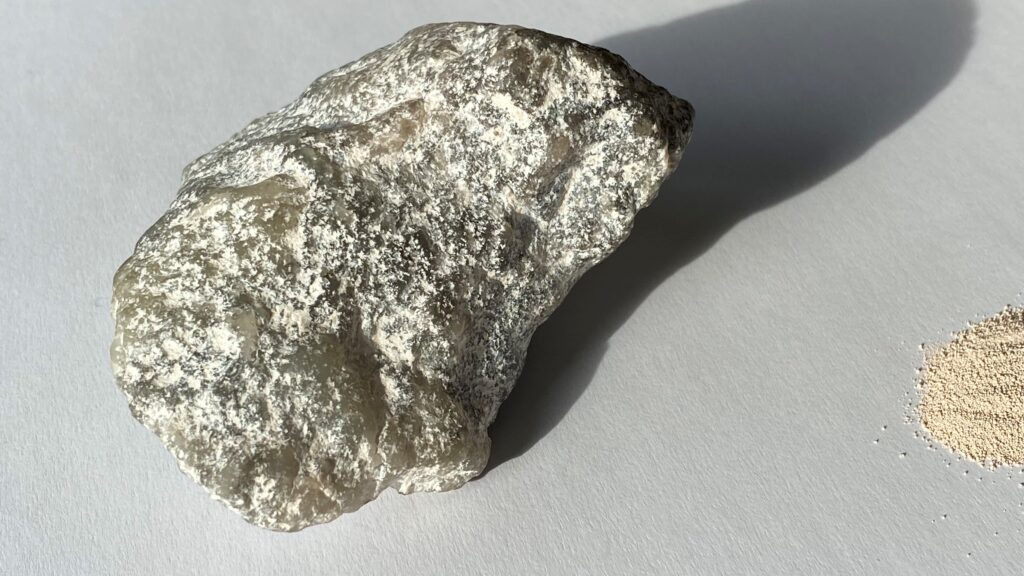
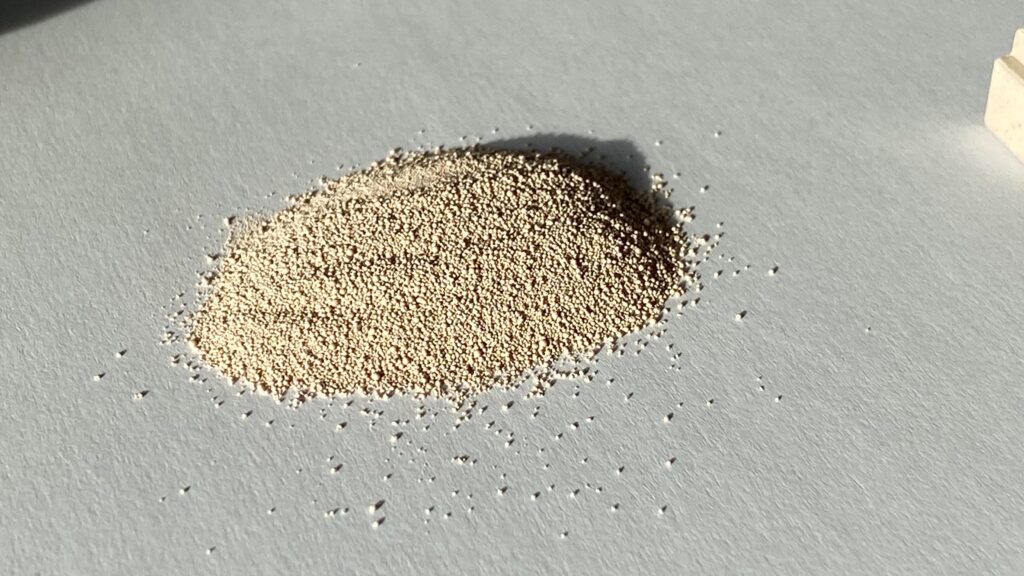
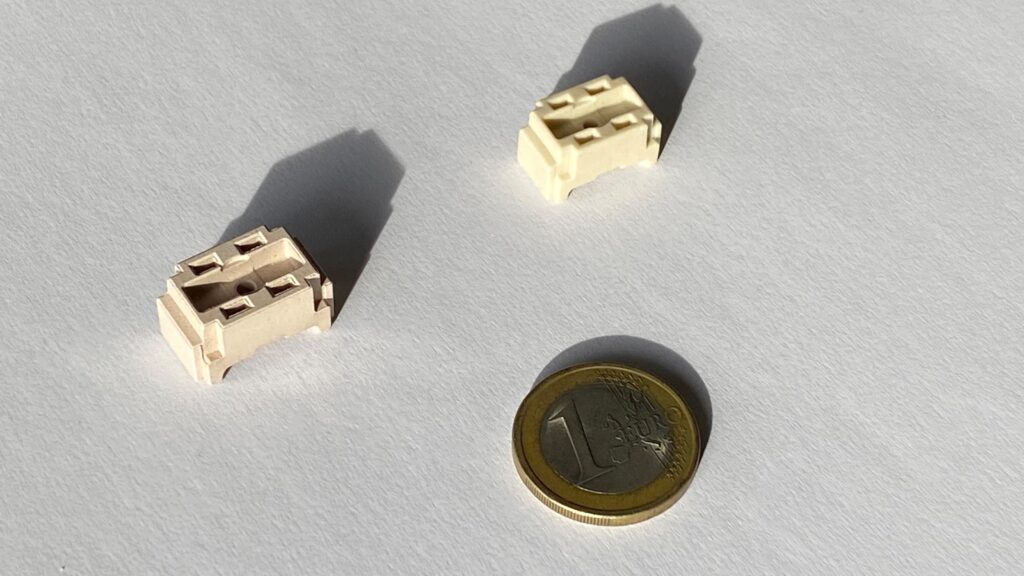
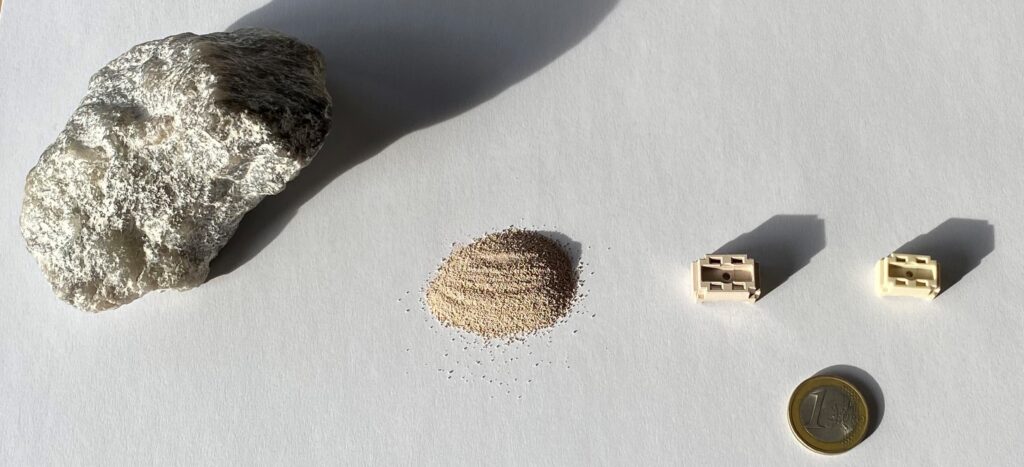
Many points speak in favour of silicate ceramics. However, one must not forget the high hardness and impact strength of oxide ceramics. This makes it extremely resistant to wear and tear as well as sudden loads and impacts. Oxide ceramics are thus ideal for applications in which components are exposed to high loads, such as in rolling bearings, combustion chambers, seals, pulleys and nozzles.
Our Conclusion
The raw materials of silicate ceramics occur naturally. In addition, preparation is cheaper and sintering temperatures are lower. From the point of view of sustainability and energy efficiency, silicate ceramics are therefore the material of choice for us.
As our name suggests, we at Steka work primarily (though not exclusively) with silicate ceramics: steatite, cordierite and technical porcelain. The details can be found in our material data sheet.