We focus on progress and automate parts of our production. Automation brings exciting challenges, particularly in the production of technical ceramics. From the sensitivity of green bodies to precise quality controls – in this blog we show why this area is so demanding and how we find solutions for it.
To mark the company’s 75th anniversary in 2024, we invested in two highly innovative, fully automated production systems. These systems enable us to overcome the challenges of manufacturing delicate ceramic components even better. In addition to the considerable increase in productivity, the use of materials has also been improved thanks to significantly less waste and the overall quality of the components. You can watch the video of the new system here.
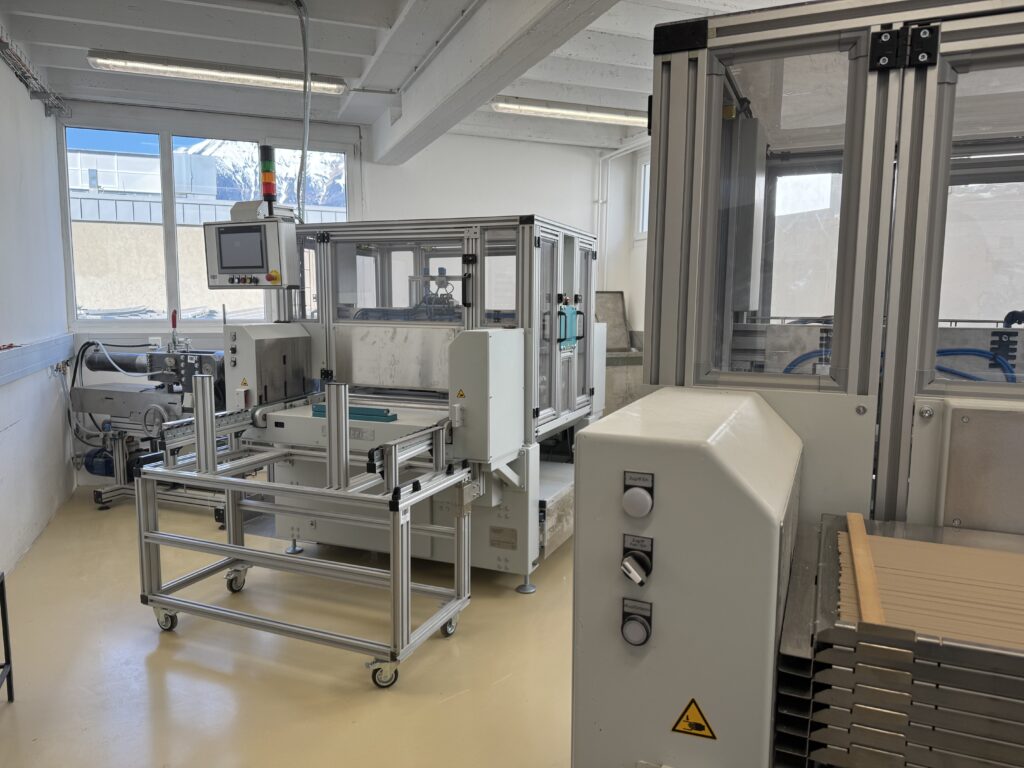
The challenges of automation
We are moving with the times and would like to automate further areas of our production. However, automation is particularly challenging for the production of technical ceramics. This is because the ‘green bodies’, i.e. the unfired or unsintered blanks, are very sensitive and can easily become deformed or cracked. Automation systems must therefore work very precisely and carefully, which requires complex robotics and sensor technology. The special material poses a major challenge for plant manufacturers. They have to think outside the box and acquire knowledge about the properties of the material.
The challenges of automation in the production of technical ceramics are due to the following factors:
Mechanical sensitivity of green compacts
Green bodies are brittle and sensitive to mechanical stress. During processing, such as during transport, handling or automated processing steps, they can easily break or crack.
Automation systems must therefore work very precisely and carefully, which requires complex robotics and sensor technology.
Heterogeneity of materials
Technical ceramics are made from a variety of materials that can vary in their composition and processing. This variability means that the properties of the green bodies (e.g. strength, porosity, moisture content) can vary.
Automation systems must be adaptable in order to deal with these material variations.
Complex geometries
Technical ceramics are often produced in complex shapes that require high precision. The moulding, pressing or injection moulding of such parts requires customised tools and machines.
Automation systems must be able to fulfil such precision requirements, which complicates their design and programming.
Drying and shrinking processes
Green compacts contain moisture that escapes during drying, leading to shrinkage and potential deformation.
Automated processes must take this into account and often react to shrinkage and geometric changes to ensure accuracy of fit and quality.
Surface sensitivity
The surface of green parts is often sensitive to scratches, marks or contamination. Defects in the surface can impair the functionality and strength of the end product.
Automated handling systems must therefore be specially designed to prevent damage.
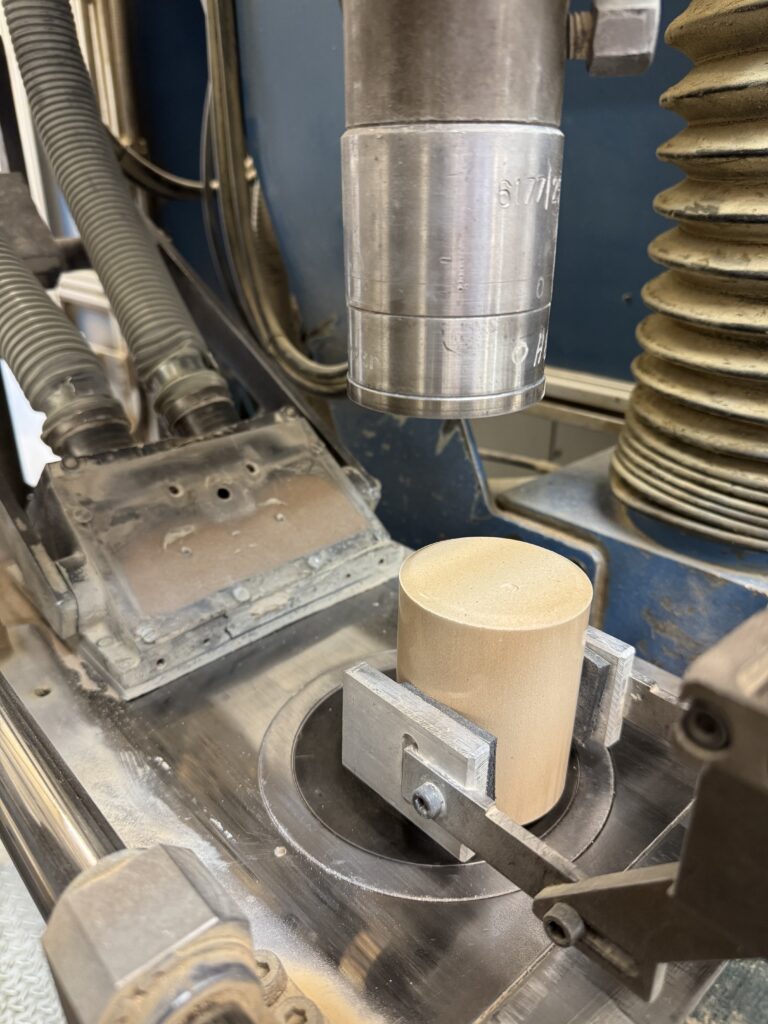
Process monitoring and quality control
Ceramic green bodies often have subtle defects such as micro-cracks or inhomogeneities that are difficult to detect. Automated quality control requires advanced technologies such as image processing systems or ultrasound-based inspections.
The implementation of such systems is technically and economically demanding.
Flexibility of production
In technical ceramics, there are often smaller production series and a wide range of individual requirements. Automation must therefore be very flexible in order to map changing product designs and processes.
Costs of automation
The series to be produced are often too small to bear the costs of automation alone. We are therefore constantly on the lookout for similar components in order to create a portfolio in which the investment in a device or machine pays off overall.
Outlook
For our production, automation not only means optimising processes, but in some cases also developing a completely new technology. Close cooperation with plant engineers is essential for us because the material is difficult and potential problems in individual process steps should ideally be recognised and prevented at the design stage. Optimisations during commissioning must also be carried out in close coordination in order to minimise the probability of errors on the one hand and to keep costs under control on the other.
We also want to drive forward research into automation in ceramic production. We are working on this together with the Robotic Centre at MCI Innsbruck. The students are analysing the potential in our production facilities and defining priorities with the aim of building a functional prototype. This will then be tested by us and mark the start of the automation offensive. We are looking forward to the first results!
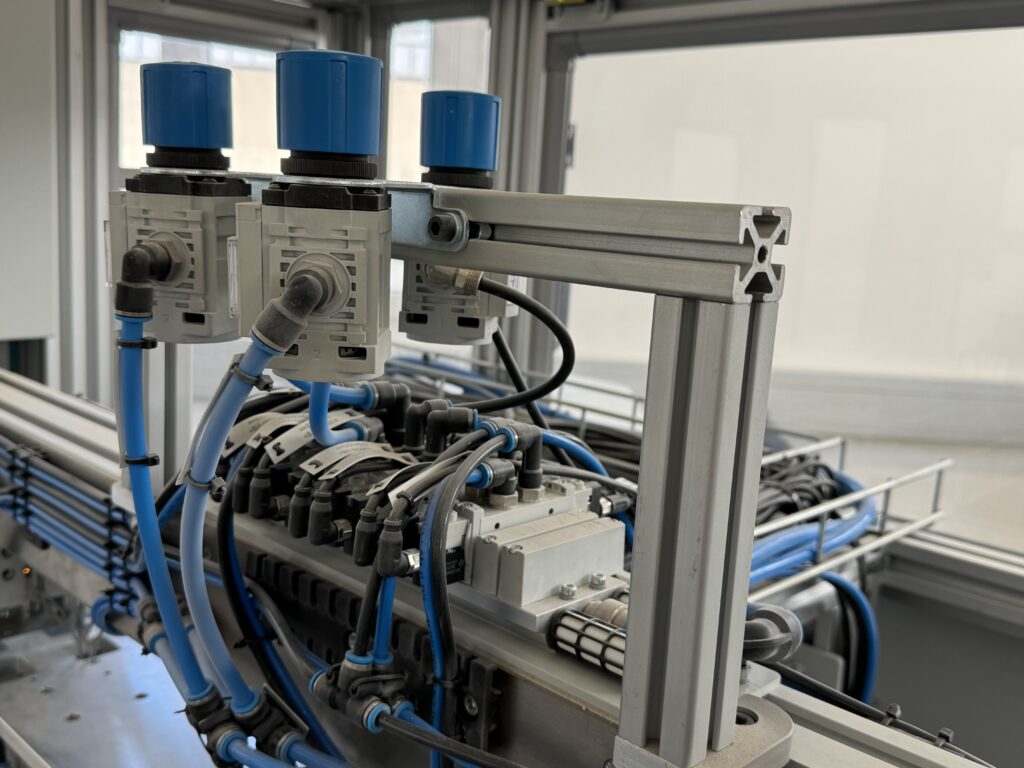
Summary: Automation in technical ceramics
Automating the production of technical ceramics, especially when handling green bodies, requires specialised technologies and precise control in order to take into account the sensitive properties of the workpieces. Close cooperation with plant manufacturers, innovative research collaborations and the development of new technologies that combine careful handling, intelligent process monitoring and adaptable machines are crucial here.