Silikatkeramik begleitet uns im Alltag und wird auch in der Industrie häufig eingesetzt: In der Hausgerätetechnik werden damit elektrische Verbindungen, Thermoelemente und Thermostate isoliert. In der Energieversorgung kommt Silikatkeramik in Drosselspulen oder Niederspannungs-Hochleistungssicherungen zum Einsatz. Poröse Silikatkeramik findet unter anderem in der Elektrowärmetechnik – etwa in Heizelementen – Anwendung. Die Gründe für die Beliebtheit des Werkstoffes sind vielfältig: Silikatkeramik ist sehr beständig, hält extremen Temperaturen sowie UV-Licht und Korrosionen stand und kann hohen mechanischen Belastungen ausgesetzt werden.
Oxidkeramik weist ähnliche positive Charaktereigenschaften auf. In Zeiten der Klimaerwärmung und der aktuellen Energiekrise lohnt sich eine Gegenüberstellung der beiden Werkstoffe. Wie schneiden Silikat- und Oxidkeramik in puncto Energieeffizienz ab?
- Die Vormaterialien zur Herstellung von Silikatkeramik, Pulver oder Granulate, werden direkt aus natürlichen, mineralischen Rohstoffen hergestellt, sind recyclebar und unter Umständen sogar biokompatibel. Oxidkeramik besteht aus synthetischen Materialien, die beispielsweise im Falle von Aluminiumoxid aus Bauxit in einem aufwändigen chemischen Verfahren gewonnen und in speziellen Öfen bei ca. 1.000°C kalziniert werden. Im Vergleich zu Oxidkeramik erfordert die Herstellung der keramischen Massen für Silikatkeramik weit weniger Energie und produziert weniger CO2-Emissionen, da lediglich bei der Herstellung des Sprühkorns Energie zur Verdampfung des Schlickers benötigt wird.
- Die Sintertemperatur von Silikatkeramik ist grundsätzlich niedriger als die von Oxidkeramik. Damit ist die Herstellung von Silikatkeramik energieeffizienter, da der Sinterprozess – also die Umwandlung vom Mineralgemenge zur dichten Keramik – schon ab einer Temperatur von ca. 900°C einsetzt. Der Sinterprozess ist bei Silikatkeramiken bei Erreichen einer Temperatur von ca. 1.300°C, und einer bestimmten Haltezeit auf dieser Temperatur, abgeschlossen. Oxidkeramiken benötigen oft Temperaturen von 1.600 bis 1.800°C. Dies führt zwangsläufig zu höheren CO2 Emissionen.
- Ein weiteres Plus ist, dass Silikatkeramik in der Regel eine bessere Wärmespeicherfähigkeit und geringe thermische Leitfähigkeit aufweist, was sie zu einer guten Wahl für Wärmeübertrager und Wärmespeicher macht. Weniger Wärmeverluste bedeuten eine höhere Energieeffizienz.
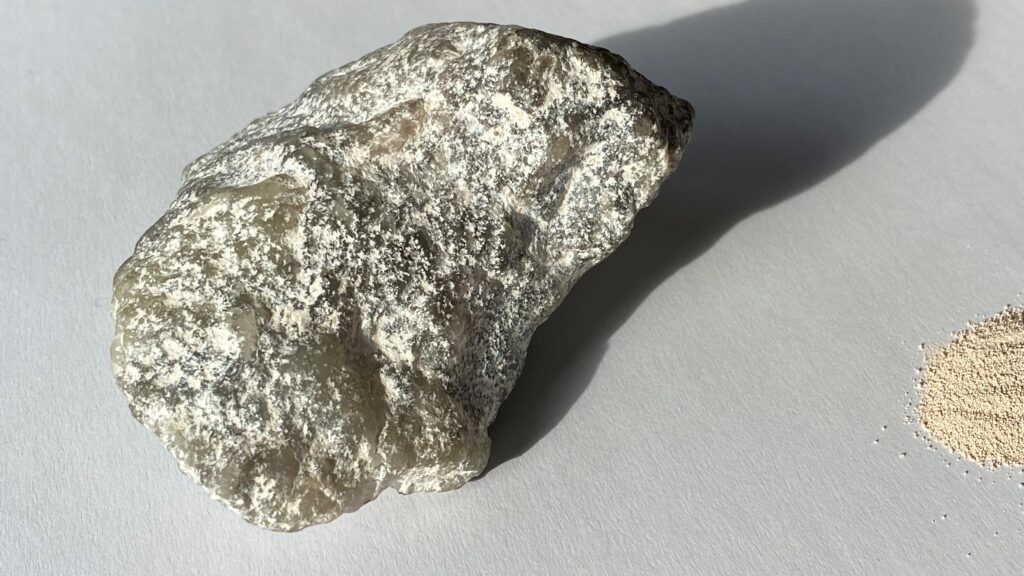
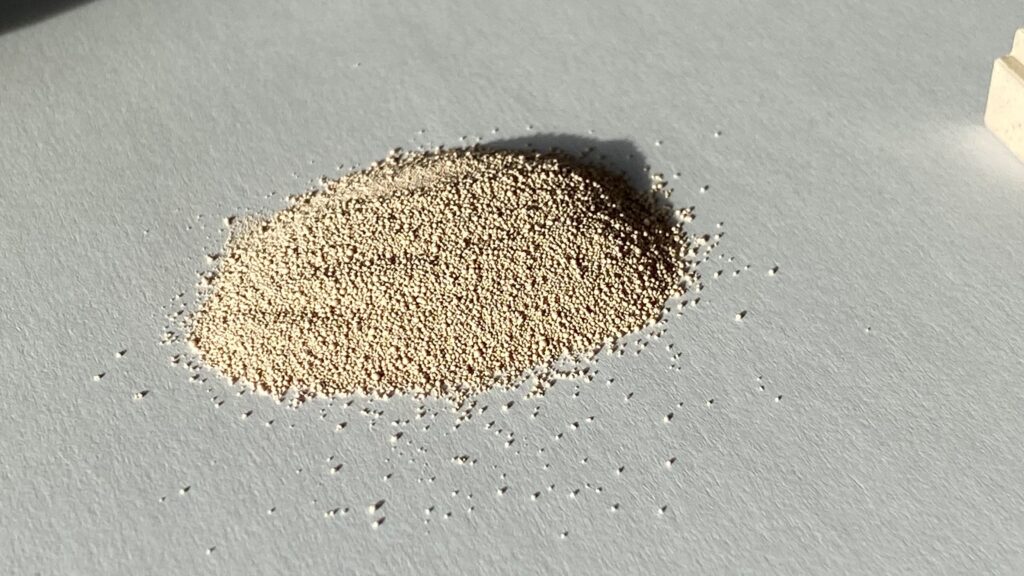
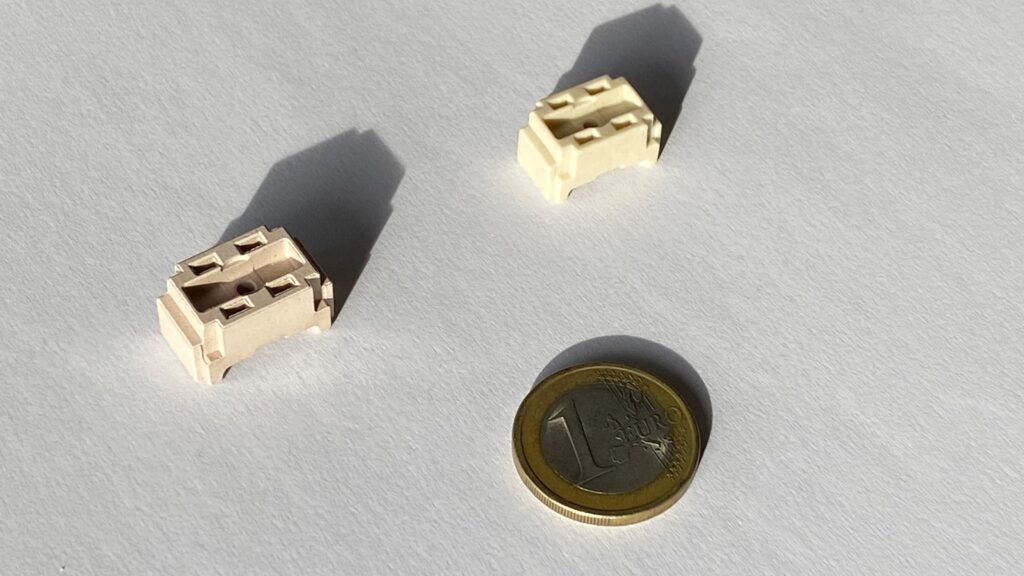
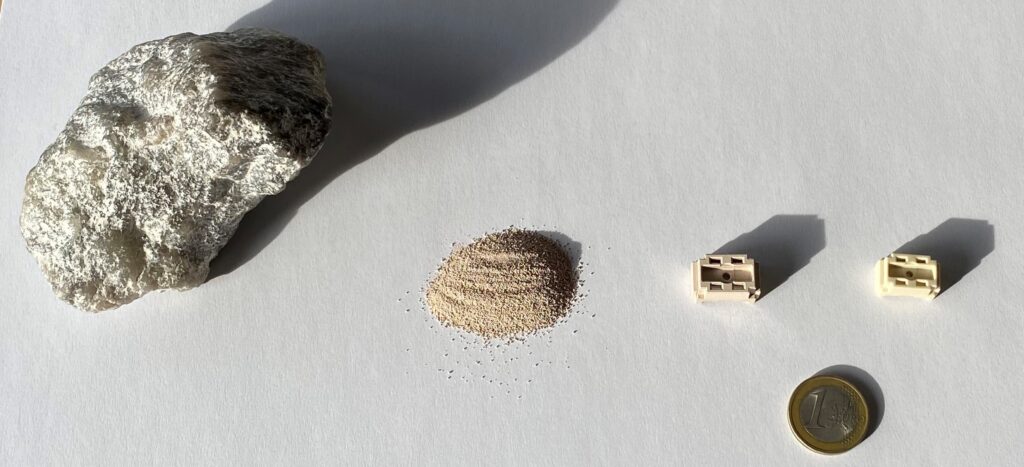
Viele Punkte sprechen für Silikatkeramik. Dabei darf man aber die hohe Härte und Schlagzähigkeit von Oxidkeramik nicht vergessen. Dadurch hat sie eine extreme Widerstandsfähigkeit gegenüber Abnutzung, Verschleiß sowie plötzlichen Belastungen und Impakten. Oxidkeramik ist damit ideal für Anwendungen, bei denen Bauteile hohen Belastungen ausgesetzt sind, wie zum Beispiel in Wälzlager, Brennkammern, Dichtungen, Riemenscheiben und Düsen.
Fazit
Die Ausgangsmaterialien von Silikatkeramik kommen in der Natur vor. Darüber hinaus ist die Aufbereitung günstiger, die Sintertemperaturen sind niedriger. Aus Sicht der Nachhaltigkeit und Energieeffizienz ist Silikatkeramik daher für uns der Werkstoff der Wahl.
Wie unser Name verrät, arbeiten wir bei der Steka vordergründig (wenn auch nicht nur) mit Silikatkeramiken: Steatit, Kordierit und technisches Porzellan. Die Details dazu finden sich in unserem Materialdatenblatt.